What is Industry 4.0: Technological Revolution and Global Transformation
- Ali
- 21 août 2024
- 7 min de lecture
22/08/2024
By Ali.

#Industry4.0 #FourthIndustrialRevolution #TechRevolution #SmartManufacturing #IoT #ArtificialIntelligence #BigData #AdditiveManufacturing #AugmentedReality #CyberPhysicalSystems #DigitalTransformation #SmartFactories #Innovation #FutureOfWork #ManufacturingTrends
Industry 4.0 (also known as the fourth industrial revolution)Â refers to the integration of new technologies into production and manufacturing processes. It represents a decisive step in industrial evolution, where digital technologies, cyber-physical systems, and the Internet of Things (IoT) are radically transforming traditional production chains.
To grasp the essence of Industry 4.0, it's useful to look back at previous industrial revolutions. The first revolution, in the 18th century, introduced mechanization with the steam engine. The second, occurring in the late 19th and early 20th centuries, brought mass production through electricity and the assembly line. The third revolution, in the mid-20th century, marked the rise of automation with computing and electronics.
Today’s era builds on these advancements by interlinking machines, systems, and processes through digital networks, giving rise to smart factories where data-driven decision-making is central. This revolution extends beyond manufacturing, affecting supply chains, logistics, and human resource management.
As this transformation continues, it holds the potential to redefine not just how products are made, but also how businesses operate in an increasingly interconnected and intelligent landscape.
The Pillars of Industry 4.0
The fourth industrial revolution is built on several key technologies that collectively form an integrated and intelligent ecosystem. These foundational elements enable businesses to modernize their processes, boost competitiveness, and adapt to market demands in real-time. Let's delve into these essential components.
The Internet of Things (IoT):Â The IoT concept involves connecting physical objects to the Internet, allowing these objects to communicate with each other and other systems. In the context of Industry 4.0, this means that machines, sensors, and other equipment within a factory can continuously exchange data, providing a real-time overview of the entire production process. This enables performance optimization, reduces downtime, and enhances predictive maintenance.
Artificial Intelligence (AI):Â AI plays a crucial role here by analyzing the data generated by IoT and automating decision-making. With sophisticated algorithms, AI can predict trends, optimize production lines, and even make real-time decisions to correct anomalies before they become major issues.
Big Data and Analytics:Â With the massive accumulation of data in smart factories, the ability to analyze this data and extract actionable insights is essential. Big Data allows for the analysis of vast volumes of data from various sources, while advanced analytics tools help identify patterns, optimize processes, and make more informed decisions.
Additive Manufacturing (3D Printing):Â Additive manufacturing, better known as 3D printing, creates objects by adding layers of material according to a digital model. This technology offers unprecedented flexibility in production, allowing for the creation of complex parts on demand, reducing prototyping costs, and economically customizing products.
Augmented Reality (AR) and Virtual Reality (VR):Â These technologies overlay digital information onto the physical world or create immersive environments. In industry, AR can be used to train workers, visualize production steps, or remotely assist technicians. VR, on the other hand, allows for the simulation of production environments, aiding in planning and training.
Cyber-Physical Systems (CPS):Â CPS are integrated systems where physical and digital elements interact in real-time. In a smart factory, this means machines can be monitored and controlled remotely via digital systems, enabling greater precision and responsiveness.
These technologies do not operate in isolation but rather in synergy, creating a hyper-connected production environment. However, to fully leverage the potential of Industry 4.0, it is crucial to understand the benefits it offers and the challenges it poses.
Benefits
The impact extends beyond merely modernizing production chains. It offers a range of benefits that transform not only how products are manufactured but also how businesses operate and interact with their environment.
Increased Productivity:Â One of the main benefits of this fourth industrial revolution is the significant increase in productivity. Through advanced automation and real-time data analysis, businesses can optimize each step of the production process. This not only speeds up production but also reduces downtime and inefficiencies.
Flexibility and Customization:Â The 4.0 facilitates large-scale personalized production. Businesses can respond to specific customer demands with increased agility, quickly modifying production lines using technologies like 3D printing and modular production systems. This flexibility also reduces costs related to small batch production or custom manufacturing.
Energy Efficiency and Waste Reduction:Â Businesses can more precisely monitor and control their energy consumption. The use of cyber-physical systems and Big Data helps identify energy inefficiencies and address them quickly. Moreover, production processes can be optimized to reduce waste, both in raw materials and non-conforming products.
Improved Quality and Reduced Errors:Â The integration of sensors and analysis systems into production processes allows for real-time quality control. This means defects can be detected and corrected instantly, even before products leave the production line. This ability to intervene early reduces the rate of defective products and enhances customer satisfaction.
These benefits illustrate the transformative potential of this revolution. However, this shift towards smarter production is not without challenges, particularly concerning cybersecurity, workforce skill adaptation, and implementation costs.
Challenges
Cybersecurity:Â With the increasing integration of connected technologies and digital systems, cybersecurity becomes a major priority. Smart factories, linking thousands of devices via IoT, are particularly vulnerable to cyberattacks. A breach can not only disrupt production but also expose sensitive data and compromise employee safety. Therefore, it is essential to develop robust cybersecurity strategies, including data protection protocols and intrusion detection systems.
Workforce Skill Adaptation:Â The shift to a connected industry requires a change in workforce skills. Traditional production jobs are evolving into roles requiring skills in computing, data analysis, and complex system maintenance. This transition demands significant efforts in training and skill development to prepare the current and future workforce for this new industrial reality.
Implementation Costs:Â Adopting Industry 4.0 technologies involves significant investments. Initial costs, including purchasing new machines, integrating digital systems, and training employees, can be high, especially for small and medium-sized enterprises. However, these investments are often necessary to remain competitive in a global market where efficiency and innovation are key. Businesses must carefully evaluate the return on investment and plan the implementation strategically.
These challenges, while significant, should not be seen as insurmountable obstacles. Instead, they can be viewed as opportunities to strengthen the resilience and adaptability of businesses. Indeed, each industry will be impacted differently by Industry 4.0, and understanding these impacts is essential to adequately prepare.
Impact on Different Sectors
Manufacturing:Â The manufacturing sector is arguably the most directly affected. Manufacturing becomes smarter with the integration of cyber-physical systems, enabling real-time, more flexible, and customized production. Production lines are optimized to reduce downtime and errors while increasing the ability to respond to specific customer demands. This transformation results in improved product quality, reduced costs, and increased global market competitiveness.
Healthcare:Â In the healthcare sector, the revolution paves the way for major innovations. Connected medical devices allow for real-time patient monitoring, improving diagnostic accuracy and treatment personalization. Additionally, analyzing Big Data from medical records and body sensors facilitates early disease detection and epidemic management. Additive manufacturing (3D printing) is increasingly used to produce custom prosthetics and implants, reducing lead times and costs.
Transport:Â The transport sector also benefits from advancements. The Internet of Things enables real-time tracking of vehicles and goods, optimizing fleet management and logistics. Autonomous vehicles, made possible by artificial intelligence and cyber-physical systems, represent a revolutionary development, promising safer, more efficient, and less polluting transport. This transformation impacts both logistics and public and private transport.
Energy:Â The energy industry is also seeing its paradigms disrupted. Smart grids allow for more efficient energy distribution, integrating renewable sources more smoothly and adapting production to real-time demand. Using data and AI for predictive maintenance of energy infrastructure reduces failures and extends equipment lifespan, while improving facility safety.
Each sector benefits from Industry 4.0 in a way unique to its needs, but the transformation is universal. However, the impact of these changes extends beyond improving current processes; it also redefines the future of industry as a whole.
The Future of Industry 4.0
The full potential is still far from being realized. The technologies underpinning it, such as artificial intelligence, Big Data, and the Internet of Things, continue to evolve rapidly. This constant development opens the door to new innovations that will further redefine the industrial landscape.
Future Innovations:Â The future may see deeper integration of artificial intelligence, not only in data analysis but also in autonomous decision-making. Next-generation AI systems will be able to self-improve through machine learning, making industrial processes even more efficient and adaptive. Additionally, the advent of 5G will enable faster and more reliable connectivity, facilitating instant communication between machines and systems on an unprecedented scale.
Impact on the Global Economy:Â Industry 4.0 will continue to play a crucial role in redefining the global economy. By making production processes more efficient, it could lead to lower manufacturing costs, making products more affordable for consumers. However, it may also exacerbate economic inequalities, particularly in regions where access to advanced technologies is limited. Businesses and governments will need to work together to ensure the benefits of this revolution are shared equitably across the globe.
Society and Employment:Â The future of the 4.0 will also impact the labor market. While some repetitive and dangerous tasks will be automated, creating safer work environments, this will also lead to a transformation in the skills required. Future jobs will demand continuous training and quick adaptation to new technologies. Companies will need to invest in employee training, while governments will need to ensure educational systems are aligned with this new industrial era.
This is not just a technological evolution; it is a societal transformation driver that will shape the future of work, business, and economies worldwide.
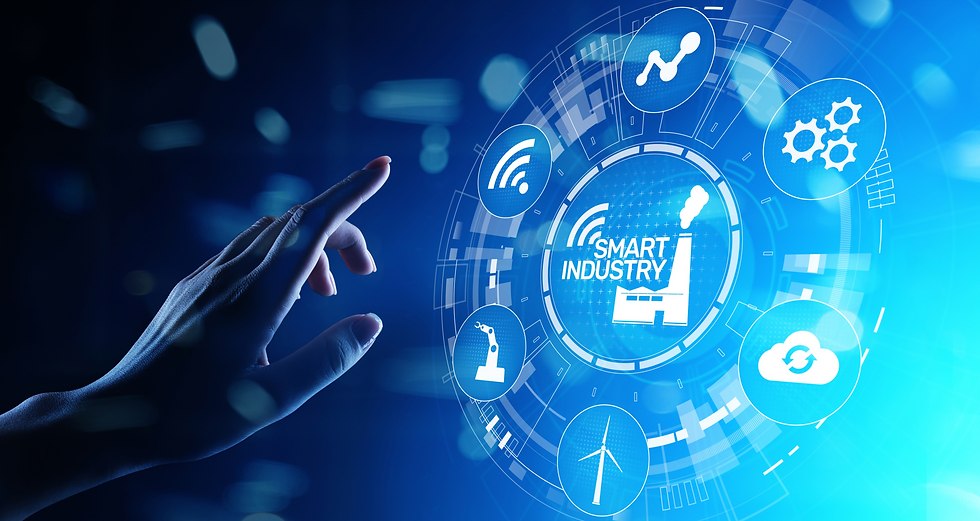
The forth Revolution marks a decisive turning point in industrial history. It combines artificial intelligence, the Internet of Things, Big Data, and other cutting-edge technologies to radically transform how businesses operate. Its impacts are felt across various sectors, from manufacturing to healthcare, transportation, and energy, each benefiting from increased productivity, enhanced flexibility, and optimized energy efficiency.
However, this revolution is not without challenges. Cybersecurity, skill adaptation, and implementation costs are major obstacles that companies must overcome to succeed in this new industrial era. Yet, these challenges also present opportunities for those who can address them with resilience and innovation.
The future looks promising, with new innovations on the horizon that will continue to redefine our economy and society. To maximize the benefits of this revolution, it is essential for businesses, governments, and individuals to work together to ensure that the impact is both positive and equitable.
Ultimately, Industry 4.0 is not just about technology; it is an invitation to rethink our approach to work, production, and society as a whole. By fully embracing this transformation, we have the opportunity to shape an industrial future that is not only more efficient but also more sustainable and inclusive.
"Industry 4.0: The Industrial Internet of Things"Â par Alasdair Gilchrist.
"The Fourth Industrial Revolution"Â par Klaus Schwab.
"Industry 4.0: A new industrial revolution - How Europe’s manufacturers can navigate the fourth industrial revolution" par McKinsey & Company.
"The Future of Manufacturing: Industry 4.0"Â par Deloitte Insights.
"Industry 4.0: Smart Manufacturing and the Digital Future"Â par PwC.
"Global Industry 4.0 Survey"Â par Siemens.
Forbes - Industry 4.0
World Economic Forum - Industry 4.0
Institute for Manufacturing - University of Cambridge
International Organization for Standardization (ISO) sur les normes relatives à l'industrie 4.0.
Automation World - Industry 4.0