The 5 trends Series: Emerging Trends in Sustainable Manufacturing to Watch in 2024
- Ali
- 3 sept. 2024
- 9 min de lecture
By Ali
04/09/2024
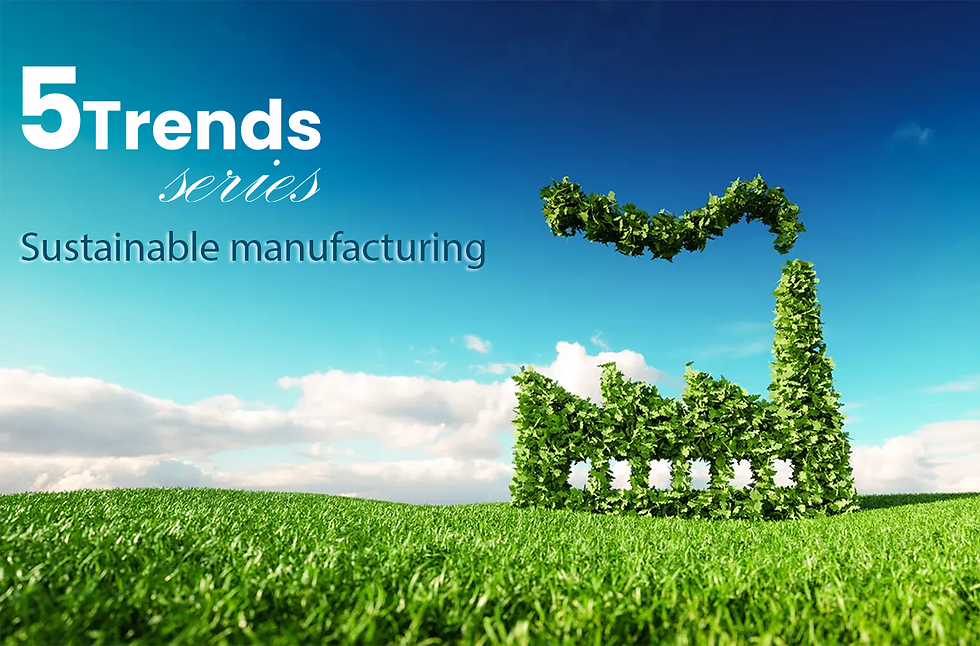
Emerging Trends in Sustainable Manufacturing to Watch in 2024
What are the 5 Emerging Trends in Sustainable Manufacturing to Watch in 2024?
1. Integration of Circular Economy in Production Processes
In the evolving landscape of sustainable manufacturing, the circular economy is making waves as a transformative force, radically redefining our approach to production and resource management. Imagine a system where products don’t merely follow a linear path from creation to disposal, but instead are reincarnated and reincorporated into the production cycle. This forward-thinking vision is becoming a reality as industries increasingly embrace circular economy principles.
At its core, the circular economy challenges the conventional "take, make, dispose" model—a system that often results in significant waste and resource depletion. Instead, it advocates for a closed-loop system where the emphasis is on prolonging the lifecycle of products and materials. This approach involves reimagining the entire product lifecycle, from design to end-of-life, with a focus on creating products that are durable, modular, and easy to disassemble. This not only facilitates repair and upgrades but also enables efficient recycling and material recovery.
One of the most exciting aspects of this shift is the advancement in recycling technologies. Innovations such as chemical recycling allow for the breaking down of end-of-life products into their raw materials, which can then be used to create new products. This reduces the dependency on virgin resources and minimizes waste. Similarly, mechanical recycling methods are being refined to handle a wider range of materials, further enhancing the efficiency of material recovery. Companies are also exploring novel business models, such as product-as-a-service, where manufacturers retain ownership of the products and are responsible for their entire lifecycle, including maintenance, repair, and eventual recycling. This model not only promotes resource efficiency but also aligns with emerging consumer expectations for sustainability.
The circular economy's impact extends beyond waste management and resource efficiency. By reducing the demand for new raw materials and optimizing the use of existing resources, companies can make significant strides in lowering their environmental impact. This approach is particularly relevant in the context of global efforts to combat climate change. As industries adopt circular practices, the benefits ripple out to include reduced carbon footprints and enhanced sustainability. The intersection of circular economy principles with broader environmental goals, such as carbon emission reduction, underscores a comprehensive strategy for achieving a greener and more resilient manufacturing sector.
As the conversation on sustainable manufacturing progresses, the integration of circular economy practices serves as a cornerstone for broader environmental strategies. The focus on reducing waste and optimizing resource use naturally complements other critical efforts, including the reduction of carbon emissions. By understanding and leveraging these interconnected strategies, manufacturers are setting the stage for a future where sustainability is not just a goal but a fundamental aspect of operational excellence.
Â
2. Reducing Carbon Emissions in Manufacturing
In the drive toward sustainability, minimizing carbon emissions has become a critical priority for manufacturers. Given that industrial activities are significant sources of greenhouse gases, reducing these emissions is essential for environmental preservation and regulatory compliance.
A key strategy for achieving this goal is to improve energy efficiency throughout production operations. By fine-tuning energy use, companies can reduce the carbon footprint associated with each unit of output. This can be achieved through various measures, such as investing in state-of-the-art machinery, enhancing thermal management, and adopting energy-saving technologies. These enhancements not only lower emissions but also result in cost savings due to decreased energy consumption.
Transitioning to renewable energy sources represents another crucial approach. Moving away from fossil fuels towards alternatives like solar, wind, and hydroelectric power can substantially cut carbon emissions. This shift often involves installing on-site renewable energy systems, such as solar panels or wind turbines, or sourcing green energy from external providers. Such changes align with broader sustainability objectives and bolster a company’s reputation for environmental stewardship.
Additionally, the adoption of carbon capture and storage (CCS) technologies offers a promising solution. CCS captures carbon dioxide emissions from industrial activities and either stores them underground or repurposes them for other uses, such as enhanced oil recovery. While CCS requires significant investment and infrastructure, it can substantially mitigate atmospheric CO2 levels.
Moreover, manufacturers are making strides by enhancing process efficiency and exploring innovative materials. Streamlining supply chains to cut down transportation emissions and using low-carbon materials can further reduce the carbon footprint. Many companies are also engaging in carbon offset initiatives, investing in projects that either reduce or sequester greenhouse gases elsewhere.
Achieving lower carbon emissions extends beyond technological upgrades and process enhancements; it involves cultivating a culture of sustainability within organizations. Setting ambitious carbon reduction goals, involving employees in green initiatives, and regularly tracking and reporting progress are crucial components of this culture. As manufacturers advance their carbon reduction efforts, these actions often synergize with other sustainability strategies, such as adopting circular economy principles.
The pursuit of reduced carbon emissions is closely linked with broader sustainability efforts. As the industry evolves, integrating carbon reduction strategies with other eco-friendly practices will be essential for long-term environmental success. Embracing a comprehensive approach to sustainability will enable manufacturers to build a more responsible and resilient future.
Â
3. Using Recycled Materials in Manufacturing
In the quest for sustainable manufacturing, the use of recycled materials is becoming increasingly prominent. This practice not only supports environmental stewardship but also contributes to resource efficiency and cost savings. By incorporating recycled materials into production processes, manufacturers can significantly reduce their reliance on virgin resources and minimize waste.
Recycling materials involves reclaiming and reprocessing discarded products into new raw materials, which can then be used to produce new goods. This process often includes the collection, sorting, and processing of materials such as metals, plastics, glass, and paper. Innovations in recycling technology are making it possible to recover high-quality materials from previously used products, which are then reintegrated into the manufacturing supply chain.
One notable advancement in this area is the development of closed-loop recycling systems. These systems are designed to continuously recycle materials within a specific production cycle, reducing the need for new inputs and minimizing waste. For example, in the automotive industry, old vehicles are dismantled, and their parts are recycled into new vehicles, creating a closed-loop system that significantly reduces material waste.
In addition to technological advancements, there is a growing trend towards the use of recycled materials in consumer goods. Products made from recycled content, such as clothing, packaging, and construction materials, are becoming more common. This shift not only helps in reducing the demand for raw materials but also raises consumer awareness about sustainability. Companies are increasingly marketing products with high recycled content as part of their commitment to environmental responsibility.
Another aspect of utilizing recycled materials is the emphasis on designing for recyclability. Manufacturers are focusing on creating products that can be easily disassembled and separated into recyclable components at the end of their life. This design approach facilitates the recycling process and ensures that materials are effectively recovered and reused.
The benefits of using recycled materials extend beyond environmental impacts. Incorporating these materials can also lead to cost savings for manufacturers. Recycled materials are often less expensive than virgin materials, and their use can reduce the costs associated with waste management and disposal. Additionally, leveraging recycled materials can enhance a company's brand image by demonstrating a commitment to sustainable practices.
As we continue to explore sustainable manufacturing practices, the integration of recycled materials stands out as a key component. This approach not only supports resource conservation and waste reduction but also aligns with broader sustainability goals. The shift towards recycling is closely connected with other environmental strategies, such as reducing carbon emissions and embracing circular economy principles.
In the next section, we will delve into how optimizing energy efficiency complements the use of recycled materials and contributes to a more sustainable manufacturing ecosystem.
4. Optimizing Energy Efficiency in Manufacturing
Energy efficiency is a fundamental aspect of sustainable manufacturing, crucial for both reducing operational expenses and minimizing environmental impacts. Companies are increasingly focusing on this area to achieve their sustainability goals and lower their carbon footprints.
Improving energy efficiency starts with a thorough analysis of energy consumption across production processes. By pinpointing areas where energy is being wasted, manufacturers can make targeted upgrades. Replacing outdated machinery with energy-efficient models, such as advanced motors and HVAC systems, can lead to significant savings and reduced energy use.
Incorporating sophisticated energy management systems is another effective approach. These systems utilize smart sensors and data analytics to monitor energy use in real-time, offering insights that help identify inefficiencies and optimize consumption. This technology enables manufacturers to implement measures that reduce energy waste and manage peak demand more effectively.
Practical energy-saving practices also play a crucial role. Adjusting production schedules to avoid running energy-intensive processes during peak periods can lower overall energy consumption. Additionally, installing energy recovery systems, like heat exchangers and combined heat and power (CHP) units, allows for the capture and reuse of waste energy, further enhancing efficiency.
Utilizing renewable energy sources contributes significantly to energy optimization. Integrating technologies such as solar panels or wind turbines helps reduce reliance on fossil fuels, cutting both energy costs and environmental impact. This shift not only aligns with sustainability goals but also offers long-term financial advantages.
Creating a culture of energy efficiency within the organization is equally important. Encouraging employees to engage in energy-saving practices, setting clear energy reduction targets, and providing regular training can drive continuous improvement. Building awareness around the importance of energy efficiency fosters a collective commitment to sustainability.
Energy efficiency is a critical component of a broader sustainable manufacturing strategy. Its benefits extend beyond cost savings and environmental impact, complementing other practices like using recycled materials and reducing carbon emissions. By integrating these approaches, manufacturers can create a more sustainable and resilient production framework.
In the next section, we’ll explore how adopting renewable energy sources further complements efforts to enhance energy efficiency, forming a cohesive approach to sustainability.
5. Adopting Renewable Energy in Manufacturing
The shift towards renewable energy is revolutionizing the manufacturing sector, offering a path to more sustainable and environmentally responsible production. By integrating renewable energy sources, manufacturers can significantly reduce their reliance on fossil fuels and lower their overall carbon emissions.
Solar energy is one of the most accessible and widely adopted renewable sources in manufacturing. Installing solar panels on factory roofs or nearby land can generate substantial amounts of electricity, offsetting the need for conventional energy sources. Solar power not only reduces greenhouse gas emissions but also provides a stable and often cost-effective energy supply.
Wind energy is another promising option for manufacturers looking to enhance their sustainability. Wind turbines can be installed on-site or in nearby locations to harness wind power. This renewable source can contribute to a significant portion of a facility’s energy needs, particularly in areas with favorable wind conditions. Wind power, like solar, helps cut carbon emissions and offers long-term energy savings.
Hydropower, derived from the flow of water, presents another viable renewable energy option. Although less commonly implemented on a small scale, it can be particularly effective in regions with access to rivers or streams. Small-scale hydro installations can provide a steady and reliable energy supply while supporting environmental goals.
Incorporating renewable energy is not just about installing new technologies; it also involves strategic planning and integration. Manufacturers often start by conducting feasibility studies to assess the potential benefits and costs of renewable energy projects. This process helps determine the most suitable technologies and the optimal scale of implementation.
Beyond individual projects, many companies are opting for power purchase agreements (PPAs) with renewable energy providers. Through PPAs, manufacturers can secure a reliable supply of renewable energy without the need for upfront investments in infrastructure. These agreements offer long-term stability and can align with corporate sustainability goals.
The transition to renewable energy also has broader implications for sustainability practices. It complements efforts to improve energy efficiency and reduce carbon emissions, creating a comprehensive approach to environmental responsibility. By aligning energy sources with sustainability goals, manufacturers enhance their overall environmental performance and strengthen their commitment to responsible production.
In conclusion, sustainable manufacturing is no longer just a strategic consideration; it has become a fundamental necessity for businesses aiming to thrive in a rapidly changing world. By integrating principles like circular economy models, reducing emissions, utilizing recycled materials, improving energy efficiency, and transitioning to renewable energy, industries are laying the groundwork for a more resilient and eco-conscious future.
The companies that take decisive steps today are not only reducing their environmental footprint but also future-proofing their operations in an increasingly sustainability-driven marketplace. Innovation, responsibility, and adaptation are the keys to forging a new path, one where both economic growth and environmental care can coexist in harmony. The momentum for sustainable manufacturing is building, and those who lead this transformation will help shape a better tomorrow.
Circular Economy: The focus on recycling, reducing waste, and reusing materials remains a cornerstone of sustainable manufacturing. Companies are shifting towards closed-loop systems to reduce reliance on virgin materials and minimize waste​ (Hexagon Blog , StartUs Insights)
Carbon Emissions Reduction: There is increasing emphasis on reducing carbon emissions, particularly through energy efficiency, renewable energy, and carbon capture technologies. Manufacturers are increasingly integrating renewable energy sources, optimizing energy use, and using carbon pricing mechanisms to drive down emissions​(https://makersrow.com/ , aPriori).
Use of Recycled Materials: The use of recycled materials continues to be a priority, especially as innovations in recycling technologies make it easier to recover high-quality materials from used products. This trend is critical for reducing environmental impact and aligning with circular economy principles​(Global IMI).
Energy Efficiency: Optimization of energy use is another major focus. Advanced technologies such as smart sensors, data-driven energy management systems, and energy recovery systems are being adopted to reduce waste and improve operational efficiency​(Hexagon Blog , aPriori).
Adoption of Renewable Energy: Manufacturers are increasingly turning to renewable energy sources such as solar and wind power. This helps reduce dependency on fossil fuels and supports long-term sustainability goals​ (https://makersrow.com/, Global IMI).