Qu'est-ce qu'une Usine Clé en Main ?
- Ali
- 25 juil. 2024
- 6 min de lecture
Dernière mise à jour : 16 avr.
By Ali.
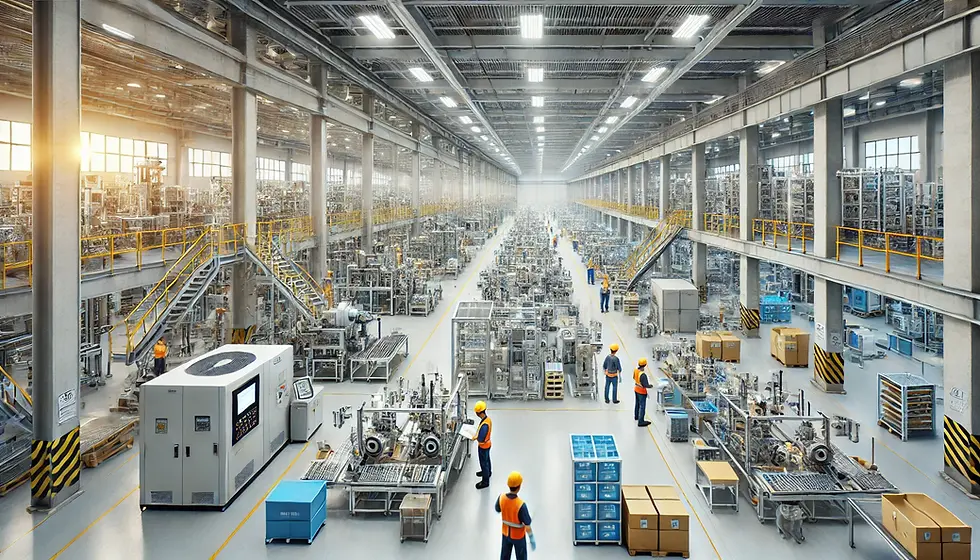
#SolutionsIndustrielles #UsineCleEnMain #GestionDeProjet #IngenierieIndustrielle #ConformiteReglementaire #FinancementProjet #InstallationEquipement #AutomatisationIndustrielle #MiseEnService #EtudeDeFaisabilite
Définition d'une usine clé en main
Une usine clé en main désigne un projet industriel dans lequel un prestataire unique prend en charge l’ensemble du processus de réalisation, depuis les études initiales jusqu’à la mise en service opérationnelle de l’installation.
Ce mode de réalisation inclut la planification, l’ingénierie, la construction, l’installation des équipements, ainsi que les essais fonctionnels. L’objectif est de fournir au client une infrastructure complète, prête à produire, sans que celui-ci ait à intervenir dans les étapes intermédiaires.
Ce type d’approche permet de réduire les risques pour le client tout en assurant une conformité stricte aux besoins, aux contraintes techniques et aux performances attendues.

1. Étude de faisabilité et conception
Avant toute chose, le projet débute par une phase de réflexion stratégique approfondie, qui constitue la base de l’ensemble du processus.
Cette étape inclut une analyse détaillée des besoins du client, tant en termes de capacité de production, de typologie de produits que d’objectifs de rentabilité. Elle prend également en compte les contraintes techniques liées aux procédés envisagés, à la disponibilité des ressources (eau, électricité, matières premières), aux conditions climatiques ou encore aux exigences en matière d’automatisation.
Parallèlement, un travail est mené sur l’environnement réglementaire local et international : normes de construction, sécurité industrielle, hygiène, gestion des déchets, conformité environnementale, etc.
L’ensemble de ces éléments permet d’élaborer un cahier des charges structuré, qui servira de fil conducteur pour l’ensemble du projet. Des plans d’implantation préliminaires sont également établis pour valider la faisabilité technique sur le site identifié, optimiser la circulation des flux et anticiper les contraintes d’exploitation.
2. Validation réglementaire et autorisations
Une fois les besoins définis et la conception amorcée, vient l’étape des démarches administratives et réglementaires. Celles-ci sont essentielles pour garantir la conformité du projet vis-à-vis des exigences légales et normatives en vigueur.
Le prestataire prend en charge l’ensemble des procédures, incluant la demande et l’obtention du permis de construire, l’analyse d’impact environnemental si nécessaire, ainsi que la mise en conformité avec les normes locales et internationales en matière de sécurité, d’hygiène, de santé au travail et de gestion des rejets.
Cette phase permet de sécuriser juridiquement le projet en amont, d’éviter tout blocage en cours de réalisation, et d’assurer que l’usine sera exploitée dans un cadre pleinement réglementé dès sa mise en service.
3. Ingénierie et dimensionnement
Les ingénieurs procèdent au dimensionnement précis des installations, en s'appuyant sur les données issues des phases précédentes. Cette étape consiste à définir, avec exactitude, les caractéristiques techniques de chaque composant de l’usine, en tenant compte des objectifs de performance, de durabilité et de sécurité.
Cela comprend le choix des technologies à utiliser, la sélection des équipements industriels, la conception des structures porteuses ainsi que l’organisation des réseaux essentiels au fonctionnement de l’usine, tels que l’électricité, l’eau, l’air comprimé, la ventilation ou les fluides techniques spécifiques.
Le résultat de ce travail d’ingénierie se traduit par la production de plans d’exécution détaillés. Ces documents servent de référence tout au long de la phase de construction et garantissent que chaque élément du projet sera réalisé conformément aux exigences fonctionnelles et réglementaires définies en amont.
4. Construction et infrastructures
L’étape de génie civil marque le début des travaux sur site. Elle englobe l’ensemble des opérations nécessaires à la préparation et à la construction de l’enveloppe physique de l’usine.
Les travaux commencent par le terrassement du terrain, suivi de la réalisation des fondations adaptées aux charges structurelles et aux caractéristiques géotechniques du sol. La structure du bâtiment est ensuite montée, qu’il s’agisse d’une charpente métallique ou béton, selon les exigences du projet.
En parallèle, les réseaux techniques enterrés ou intégrés sont mis en place : alimentation électrique, réseaux d’eau, évacuation des eaux usées, gaines techniques, systèmes de drainage, etc. Enfin, les revêtements de sol, les murs, les isolations thermiques ou acoustiques, ainsi que les aménagements intérieurs sont réalisés afin de préparer l’espace à l’installation des équipements.
Cette phase garantit que l’environnement bâti est conforme aux normes en vigueur et parfaitement adapté à l’intégration des machines, tout en anticipant les besoins futurs en matière d’entretien et d’exploitation.
5. Logistique et transport des équipements
Une fois les infrastructures prêtes, débute la phase logistique liée à l’acheminement des équipements industriels. Les machines et lignes de production, sélectionnées en fonction des spécifications techniques du projet, sont acquises auprès de fournisseurs qualifiés. Si nécessaire, des tests de pré-validation sont réalisés en usine avant expédition, afin de garantir leur conformité et leur bon fonctionnement.
Le transport est ensuite organisé selon les contraintes spécifiques des équipements : dimensions hors gabarit, exigences en matière de manutention, conditions de stockage et de sécurité. Cette étape inclut également les procédures de dédouanement à l’importation, ainsi que la gestion des documents logistiques.
La coordination des délais est essentielle à ce stade, car l’arrivée des équipements sur site doit s’aligner précisément avec l’avancement du chantier. Une mauvaise synchronisation pourrait entraîner des retards ou des surcoûts. Une attention particulière est donc portée à la planification du transport, au suivi des expéditions, et à la préparation du site pour la réception des colis.
6. Installation, câblage et mise en service
Une fois les équipements livrés, s’ouvre la phase d’installation sur site. Les machines sont positionnées selon les plans d’implantation, fixées aux structures prévues à cet effet, puis raccordées aux réseaux techniques : alimentation électrique, circuits hydrauliques, air comprimé, systèmes de commande, sécurité, etc.
L’ensemble des équipements est ensuite configuré et synchronisé pour garantir une cohérence opérationnelle entre les différentes lignes de production et les systèmes de contrôle automatisés. Cette phase nécessite souvent l’intervention d’équipes techniques spécialisées, en collaboration étroite avec les fournisseurs des machines.
Des essais à vide sont d’abord réalisés pour vérifier le bon fonctionnement mécanique et électrique de chaque unité. Viennent ensuite les tests de production en conditions réelles, avec des matières premières simulées ou réelles, afin de valider la performance, la sécurité et la conformité du système global.
Cette étape est cruciale pour identifier d’éventuels ajustements techniques et garantir que l’ensemble de l’installation répond aux objectifs définis en amont du projet.
7. Formation et transfert d’exploitation
Lorsque l’usine est entièrement opérationnelle sur le plan technique, la dernière phase du projet consiste à assurer le transfert de compétences vers les équipes du client.
Une formation complète est dispensée aux opérateurs, techniciens de maintenance et responsables de production. Elle couvre l’utilisation des équipements, les procédures de démarrage et d’arrêt, les protocoles de maintenance préventive et corrective, ainsi que les consignes de sécurité et d’hygiène industrielle.
Des supports techniques, manuels d’utilisation et procédures internes sont remis afin de garantir une autonomie rapide des équipes sur le terrain.
À l’issue de cette phase, l’exploitation de l’usine est officiellement transférée au client. Celui-ci dispose alors d’une installation prête à fonctionner, maîtrisée par son personnel, et conforme aux objectifs de performance et de qualité initialement définis. La production peut démarrer sans délai, dans des conditions optimales de sécurité et d’efficacité.
Avantages d'une Usine Clé en Main
Le modèle clé en main offre une série d’avantages significatifs en matière de gestion de projet industriel.
Tout d’abord, il permet au client de s’appuyer sur un interlocuteur unique tout au long du processus, de la conception à la mise en service. Cette centralisation facilite la coordination, limite les risques de malentendus et accélère la prise de décision.
Par ailleurs, en confiant l’ensemble des étapes à un seul prestataire, les responsabilités sont clairement définies, ce qui renforce la maîtrise de la qualité et des délais. Le fournisseur est contractuellement engagé sur les performances globales de l’installation.
Enfin, le pilotage intégré du projet permet un suivi précis des coûts, réduisant ainsi les risques de dérive budgétaire. Le client bénéficie d’une visibilité claire sur les investissements nécessaires dès le lancement du projet.
Voir la vidéo
FAQ
Quels sont les secteurs concernés ?Le modèle clé en main s’applique à de nombreux secteurs : agroalimentaire, énergie, textile, recyclage, pharmaceutique, chimie, etc.
Quel est l’intérêt d’un projet clé en main pour un investisseur ? Il permet de sécuriser l’investissement en réduisant les risques techniques et financiers. L’investisseur garde une maîtrise budgétaire et bénéficie d’un délai d’exécution optimisé.
Le client peut-il personnaliser son usine ?Oui. Même si le prestataire gère l’ensemble du projet, la conception est toujours adaptée aux besoins spécifiques du client : capacité, automatisation, process, normes locales, etc.
Est-ce plus cher qu’un projet classique ? Absolument pas. La centralisation permet des économies d’échelle, une meilleure maîtrise des coûts et une réduction des imprévus. À long terme, c’est souvent plus rentable.
Qui assure la maintenance de l’usine une fois livrée ?Cela dépend du contrat. Certains prestataires incluent une offre de maintenance post-livraison, en option ou intégrée au projet.
Quelle est la durée moyenne pour la réalisation d’une usine clé en main ?Tout dépend de la complexité du projet, mais on peut estimer une durée moyenne de 6 à 18 mois, incluant les phases d’étude, de construction et de mise en service.
Comments