Maintenance Industrielle : une problématique plus que d'actualité
- Ali
- 28 août 2024
- 10 min de lecture
29/8/2024
By Ali.
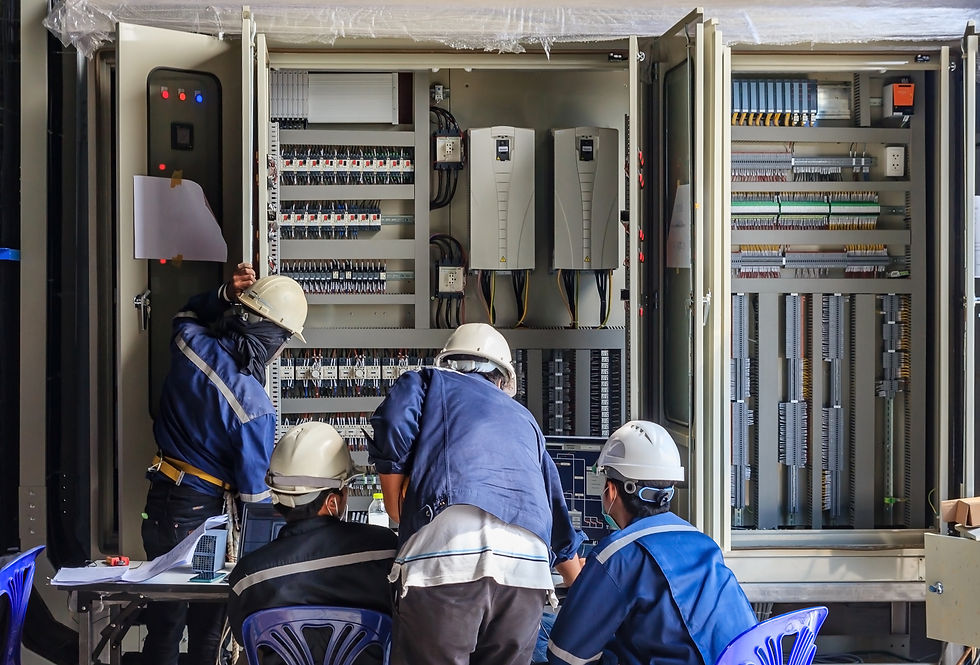
#MaintenanceIndustrielle #MaintenancePréventive #MaintenancePrédictive #MaintenanceProactive #InspectionUsine #FiabilitéÉquipements #EfficacitéIndustrielle #StratégieMaintenance #ExcellenceOpérationnelle #IoT #BigData #CMMS #IndustrieManufacturière #TravailDesTechniciens #InnovationIndustrielle
Maintenance industrielle : une problématique plus que d'actualité
Dans le monde industriel d'aujourd'hui, où chaque minute d'arrêt coûte cher et où la performance des machines est cruciale, la maintenance industrielle est devenue un enjeu stratégique. Autrefois perçue comme une simple nécessité opérationnelle, elle s'est transformée en un levier essentiel pour garantir la continuité et l'efficacité des processus de production. Les méthodes traditionnelles de réparation après panne, bien que toujours présentes, ne suffisent plus à répondre aux exigences croissantes d'un marché globalisé. Désormais, la maintenance préventive et prédictive se hissent au premier plan, offrant aux entreprises des moyens sophistiqués pour anticiper les défaillances et optimiser leurs ressources. Mais qu'est-ce qui fait de la maintenance une problématique si pressante aujourd'hui ? Cet article explore les défis et les solutions modernes qui redéfinissent la manière dont nous envisageons la maintenance industrielle.
Partie 1 : Les Fondements et Défis de la Maintenance Industrielle Traditionnelle.
La complexité de la maintenance industrielle : Une vue d'ensemble
La maintenance industrielle est un pilier fondamental pour assurer la continuité des opérations dans les environnements de production. Cette discipline englobe une gamme étendue d'activités, allant de la maintenance corrective, qui intervient après la survenue d'une panne, à la maintenance préventive, qui vise à éviter ces pannes grâce à des actions planifiées. Historiquement, la maintenance corrective a dominé les pratiques industrielles, souvent perçue comme la solution la plus économique à court terme. Cependant, les arrêts imprévus et les coûts associés aux réparations d'urgence ont rapidement démontré les limites de cette approche.
Maintenance corrective : Quand la réactivité coûte cher
La maintenance corrective, bien qu'essentielle, expose les entreprises à des risques importants. Lorsqu'une machine tombe en panne, les coûts ne se limitent pas seulement aux réparations, mais incluent également les pertes de production, les retards dans les livraisons, et parfois même la perte de clients. Ce modèle réactif peut entraîner des arrêts prolongés, car la détection tardive des pannes oblige souvent à des interventions d'urgence, souvent plus coûteuses que les réparations planifiées. En outre, l'absence de suivi régulier des équipements peut conduire à une usure accélérée et à une diminution de la durée de vie des machines.
Maintenance préventive : Un investissement dans la continuité
Pour contrer les inconvénients de la maintenance corrective, les industries ont progressivement adopté la maintenance préventive. Cette approche proactive repose sur l'idée que l'inspection régulière et le remplacement programmé des composants peuvent prévenir les pannes avant qu'elles ne surviennent. Les avantages de cette méthode sont multiples : elle permet de réduire les arrêts non planifiés, d'améliorer la fiabilité des équipements, et d'optimiser l'utilisation des ressources. Les interventions sont planifiées selon des calendriers prédéfinis ou en fonction de l'utilisation des équipements, ce qui permet de mieux gérer les ressources humaines et matérielles. Cependant, cette approche n'est pas sans ses défis. En effet, la planification basée sur des intervalles fixes peut parfois mener à des interventions inutiles, tandis qu'une mauvaise interprétation des données peut laisser passer des signes avant-coureurs de défaillances majeures.
Les limites et les défis de la maintenance traditionnelle
Malgré ses nombreux avantages, la maintenance préventive n'est pas une solution miracle. Un des principaux défis est de déterminer avec précision le moment où une intervention est nécessaire. De plus, cette approche nécessite une planification rigoureuse et une gestion optimale des ressources pour être efficace. Les entreprises doivent investir dans la formation des techniciens, l'acquisition d'outils de diagnostic, et la mise en place de systèmes de suivi rigoureux. Un autre défi majeur est lié à l'évolution rapide des technologies et des attentes du marché. Les machines sont de plus en plus sophistiquées, et les temps de réponse doivent être raccourcis pour répondre aux exigences des clients. Dans ce contexte, la maintenance traditionnelle, même en version préventive, peut parfois paraître insuffisante pour garantir une disponibilité maximale des équipements.
Vers une transition nécessaire : L'émergence de nouvelles stratégies
Face aux limites de la maintenance corrective et préventive, de nouvelles approches, comme la maintenance prédictive, ont vu le jour. Celles-ci s'appuient sur l'analyse des données en temps réel pour anticiper les pannes avant qu'elles ne se produisent. En combinant les meilleures pratiques des stratégies traditionnelles avec les innovations technologiques modernes, les entreprises peuvent non seulement réduire les coûts, mais aussi améliorer la fiabilité et la durabilité de leurs équipements. Cette évolution montre que, si la maintenance industrielle traditionnelle a longtemps été un socle solide, il est désormais temps d'intégrer des méthodes plus avancées pour répondre aux défis actuels et futurs de l'industrie.
Partie 2 : La Maintenance Préventive et Prédictive – Des Pilons pour l'Industrie Moderne
Maintenance préventive : L’art d’éviter l’inévitable
La maintenance préventive est devenue une norme dans de nombreuses industries, surpassant largement les approches réactives de la maintenance corrective. Le principe fondamental de la maintenance préventive repose sur la réalisation d'inspections, de nettoyages, et de remplacements planifiés pour prévenir les défaillances avant qu'elles ne surviennent. Cette stratégie se base sur deux approches principales : la maintenance basée sur le temps (time-based) et la maintenance basée sur l'utilisation (usage-based).
Maintenance basée sur le temps : Une régularité calculée
La maintenance basée sur le temps implique des interventions à intervalles réguliers, tels que des inspections mensuelles ou annuelles, indépendamment de l’état réel des machines. Cette approche garantit que les équipements reçoivent l'attention nécessaire avant que des problèmes graves ne surviennent. Par exemple, le remplacement des composants selon un calendrier fixe, même s'ils semblent encore fonctionnels, peut prolonger la durée de vie de la machine et prévenir les défaillances soudaines.
Maintenance basée sur l'utilisation : Ajustement selon la charge
À l'inverse, la maintenance basée sur l'utilisation intervient en fonction des cycles de fonctionnement de l'équipement ou de ses heures d’utilisation. Cette approche est particulièrement utile dans les environnements où les machines ne fonctionnent pas en continu, permettant ainsi d'adapter la fréquence des interventions en fonction de l’utilisation réelle des équipements. Par exemple, une machine utilisée sporadiquement nécessitera moins de maintenance qu'une machine en fonctionnement continu, ce qui permet d'optimiser les ressources.
Maintenance prédictive : Quand la technologie se met au service de la prévention
Avec l'évolution rapide des technologies, la maintenance prédictive est devenue un atout majeur pour les entreprises cherchant à optimiser leurs opérations. Contrairement à la maintenance préventive, qui repose sur des intervalles fixes ou sur l’utilisation, la maintenance prédictive utilise des données en temps réel pour prévoir les pannes avant qu'elles ne surviennent. Grâce à des capteurs et à des technologies de surveillance avancées, les entreprises peuvent désormais surveiller l'état des équipements en continu, détecter les anomalies et intervenir avant que la situation ne se détériore.
Technologies au cœur de la maintenance prédictive
La maintenance prédictive s’appuie sur une multitude de technologies avancées, telles que l'Internet des objets industriel (IIoT), l'analyse des big data, et l'apprentissage automatique (machine learning). Les capteurs placés sur les machines collectent en permanence des données sur divers paramètres, tels que les vibrations, la température, et la pression. Ces données sont ensuite analysées pour détecter des tendances ou des anomalies qui pourraient indiquer une défaillance imminente. En identifiant ces signaux d’alerte, les équipes de maintenance peuvent planifier des interventions ciblées, minimisant ainsi les arrêts de production et réduisant les coûts associés aux réparations d’urgence.
Avantages économiques et opérationnels de la maintenance prédictive
L’un des avantages les plus significatifs de la maintenance prédictive est la réduction des coûts opérationnels. En permettant aux entreprises de prévoir et de prévenir les pannes, cette approche réduit considérablement les interruptions non planifiées et les coûts associés aux réparations d'urgence. De plus, la maintenance prédictive prolonge la durée de vie des équipements, améliore leur fiabilité, et optimise l'utilisation des ressources humaines et matérielles. Au-delà des économies directes, cette approche améliore également la qualité des produits et la satisfaction des clients en assurant une production plus stable et sans interruptions.
L'intégration de la maintenance prédictive : Défis et solutions
Bien que les avantages de la maintenance prédictive soient clairs, son intégration n’est pas sans défis. La mise en place de systèmes de surveillance en temps réel et l'analyse des données requièrent des investissements substantiels en technologie et en formation. De plus, la gestion des données collectées, souvent massives et complexes, nécessite des compétences avancées en analyse et en interprétation. Cependant, les entreprises qui réussissent à surmonter ces obstacles se retrouvent avec un système de maintenance extrêmement efficace, capable de transformer la gestion des actifs industriels.
Partie 3 : L'intégration de la maintenance dans une stratégie industrielle moderne
L’émergence de la maintenance proactive : Une nouvelle ère pour l'industrie
La maintenance proactive se distingue comme une évolution naturelle des pratiques préventives et prédictives, intégrant les meilleures pratiques des deux mondes tout en adoptant une approche encore plus stratégique. En s’appuyant sur l’analyse des causes profondes des défaillances et sur une planification rigoureuse, la maintenance proactive vise à éliminer les risques avant même qu'ils ne se matérialisent. Cette méthode, souvent alignée avec les principes de la Maintenance Centrée sur la Fiabilité (Reliability-Centered Maintenance, RCM), est particulièrement efficace pour identifier et traiter les points de défaillance critiques dans un système industriel.
Maintenance centrée sur la fiabilité (RCM) : Une stratégie axée sur la performance
La RCM est une approche méthodique qui priorise les actions de maintenance en fonction de leur impact sur la sécurité, la production, et les coûts. Elle se concentre sur l'optimisation des processus de maintenance pour maximiser la fiabilité et l'efficacité des équipements critiques. En analysant systématiquement chaque pièce d'équipement, la RCM permet de développer des stratégies spécifiques qui répondent aux besoins particuliers de chaque machine. Ce processus implique une évaluation approfondie pour anticiper les modes de défaillance, identifier les causes potentielles, et mettre en place des mesures correctives adaptées.
L'importance de l'analyse des causes racines
Un élément clé de la maintenance proactive est l'analyse des causes racines (Root Cause Analysis, RCA). Cette méthode permet d'aller au-delà des simples symptômes pour identifier les véritables causes des défaillances. En traitant ces causes à la source, il est possible de prévenir les récidives et d'améliorer la fiabilité globale des systèmes. La RCA est souvent intégrée dans les stratégies de maintenance proactive pour assurer une amélioration continue des performances des équipements.
L'amélioration continue : Un pilier de la maintenance proactive
L’amélioration continue est un concept central de la maintenance proactive. Elle consiste à intégrer des retours d'expérience et des données de performance dans le cycle de maintenance pour affiner constamment les stratégies en place. Cela implique une surveillance régulière des équipements, l’analyse des défaillances passées, et l’ajustement des procédures de maintenance en conséquence. Grâce à cette approche, les entreprises peuvent non seulement maintenir, mais aussi améliorer la performance et la fiabilité de leurs équipements au fil du temps.
L’intégration des nouvelles technologies dans la maintenance proactive
Les avancées technologiques jouent un rôle crucial dans l’optimisation de la maintenance proactive. L'utilisation de capteurs connectés, d’outils d’analyse de données, et de systèmes de gestion de la maintenance assistée par ordinateur (CMMS) permet aux entreprises de mieux surveiller et gérer leurs équipements. Ces technologies offrent une visibilité accrue sur l’état des machines, facilitant ainsi la planification des interventions et la prévention des pannes. L'intégration de ces outils dans une stratégie de maintenance proactive est essentielle pour maximiser l'efficacité et minimiser les coûts liés aux arrêts non planifiés.
Les défis de la mise en œuvre de la maintenance proactive
Malgré ses nombreux avantages, l'adoption de la maintenance proactive pose des défis considérables. La complexité de la mise en œuvre d'une telle stratégie nécessite un investissement important en termes de formation, de technologie, et de gestion du changement. De plus, il est crucial de disposer de données précises et fiables pour que la maintenance proactive soit efficace. Cela demande une infrastructure de collecte et d'analyse de données robuste, ainsi qu'une collaboration étroite entre les équipes de maintenance et les autres départements de l'entreprise.
Vers une maintenance totalement intégrée
L'avenir de la maintenance industrielle se dirige vers une intégration complète des différentes approches de maintenance (préventive, prédictive, et proactive) dans une stratégie cohérente et globale. Cette intégration permet non seulement de maximiser la disponibilité des équipements, mais aussi d'optimiser les coûts et d'améliorer la satisfaction client. En adoptant une approche holistique de la maintenance, les entreprises peuvent non seulement prévenir les pannes, mais aussi créer un environnement de production plus résilient et agile, prêt à relever les défis de l'industrie moderne.
Réinventer la Maintenance Industrielle pour l’Avenir
Dans un monde où chaque seconde de production compte, la maintenance industrielle se révèle plus cruciale que jamais. Si les méthodes traditionnelles ont pavé la voie, elles montrent aujourd'hui leurs limites face aux défis contemporains. La maintenance préventive, avec son approche proactive, et la maintenance prédictive, armée de technologies de pointe, nous ont permis de franchir un nouveau cap, celui de l’anticipation plutôt que de la simple réaction.
Mais l'avenir appartient à ceux qui oseront aller plus loin, en intégrant une stratégie de maintenance proactive, où l'analyse des causes racines et l'amélioration continue sont des mantras. Cette approche ne se contente pas de prévenir les pannes, elle vise à les éradiquer à leur source, à transformer la maintenance en un véritable levier de performance industrielle.
L'ère des réparations après coup est révolue. Désormais, la maintenance n'est plus un simple service de support, mais une composante stratégique essentielle pour garantir la compétitivité des entreprises. Avec l'essor des technologies telles que l'IoT, l'analyse des big data, et les systèmes de gestion assistée par ordinateur, nous sommes à l'aube d'une révolution où la maintenance devient synonyme de fiabilité, de résilience, et d’innovation.
Ainsi, la maintenance industrielle, qu'elle soit préventive, prédictive ou proactive, n'est pas seulement une réponse aux défis du présent. Elle est une invitation à repenser nos infrastructures, à embrasser l'innovation, et à bâtir un avenir où les machines ne sont plus des sources d'inquiétude, mais des partenaires fiables dans la quête de l'excellence opérationnelle. L'avenir de l'industrie ne sera pas seulement déterminé par ce que nous produisons, mais par la manière dont nous assurons la continuité et la performance de nos outils de production.
C'est là que réside le véritable pouvoir de la maintenance : transformer l'incertitude en opportunité, et faire de chaque intervention une chance de s'améliorer, de progresser, et de se préparer pour les défis de demain.
DIMO Maint - "Effective strategies for industrial maintenance management," une ressource complète qui discute des stratégies optimales pour la gestion de la maintenance industrielle, y compris la maintenance préventive, corrective et prédictive. Ce site met en lumière l'importance de l'approche prédictive et l'intégration des systèmes de gestion assistée par ordinateur (CMMS).
Sensemore - "What Is Industrial Maintenance? A Complete Overview," un article détaillé qui offre une vue d'ensemble complète de la maintenance industrielle, expliquant les principes de la maintenance préventive, prédictive, et proactive, ainsi que l'importance de l'analyse des causes racines et de l'amélioration continue dans le cadre de la maintenance industrielle moderne.
Comments