Industrial Maintenance: A Timely Issue
- Ali
- 28 août 2024
- 8 min de lecture
29/8/2024
By Ali.
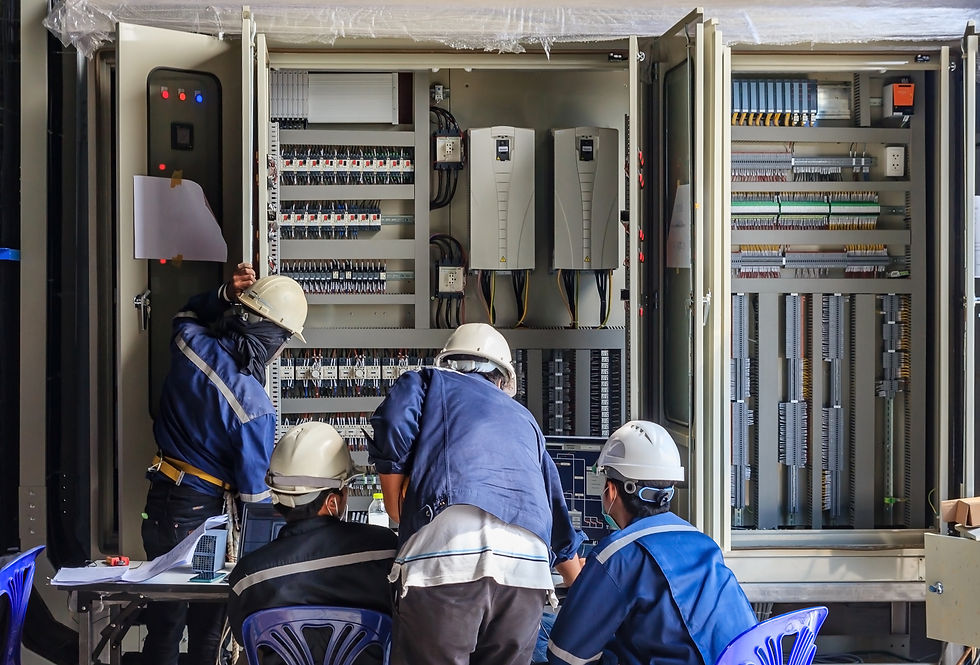
#IndustrialMaintenance #PreventiveMaintenance #PredictiveMaintenance #ProactiveMaintenance #FactoryInspection #EquipmentReliability #IndustrialEfficiency #MaintenanceStrategy #OperationalExcellence #IoT #BigData #CMMS #ManufacturingIndustry #TechnicianWork #IndustryInnovation
Industrial Maintenance: A Timely Issue
In today’s industrial landscape, where every minute of downtime can be costly and machine performance is critical, industrial maintenance has become a strategic priority. Once viewed as a mere operational necessity, it has now evolved into a crucial lever for ensuring continuity and efficiency in production processes. Traditional methods of repair after failure, though still in use, no longer suffice to meet the growing demands of a globalized market. Preventive and predictive maintenance have risen to prominence, offering businesses sophisticated means to anticipate breakdowns and optimize their resources. But what makes maintenance such a pressing issue today? This article delves into the challenges and modern solutions that are redefining the way we approach industrial maintenance.
Â
The Foundations and Challenges of Traditional Industrial Maintenance
The Complexity of Industrial Maintenance: An Overview
Industrial maintenance is a fundamental pillar for ensuring the continuity of operations in production environments. This discipline encompasses a wide range of activities, from corrective maintenance, which occurs after a breakdown, to preventive maintenance, aimed at preventing such failures through scheduled actions. Historically, corrective maintenance has dominated industrial practices, often perceived as the most cost-effective solution in the short term. However, unplanned downtime and the associated repair costs have quickly highlighted the limitations of this approach​.
Corrective Maintenance: When Reactivity Becomes Expensive
Corrective maintenance, while essential, exposes companies to significant risks. When a machine breaks down, the costs are not limited to repairs but also include production losses, delivery delays, and sometimes even the loss of customers. This reactive model can lead to prolonged downtimes, as late detection of failures often requires emergency interventions that are usually more expensive than planned repairs. Moreover, the lack of regular monitoring can accelerate wear and tear, reducing the overall lifespan of machines​.
Preventive Maintenance: An Investment in Continuity
To counter the disadvantages of corrective maintenance, industries have gradually adopted preventive maintenance. This proactive approach is based on the idea that regular inspections and scheduled component replacements can prevent failures before they occur. The benefits of this method are numerous: it reduces unplanned downtime, improves equipment reliability, and optimizes resource utilization. Interventions are scheduled based on fixed timelines or equipment usage, allowing for better management of human and material resources. However, this approach is not without its challenges. Planning based on fixed intervals can sometimes lead to unnecessary interventions, while a misinterpretation of data might overlook critical signs of impending failures​.
The Limitations and Challenges of Traditional Maintenance
Despite its many advantages, preventive maintenance is not a panacea. One of the main challenges is accurately determining when an intervention is necessary. Additionally, this approach requires rigorous planning and optimal resource management to be effective. Companies must invest in technician training, diagnostic tools, and the implementation of robust tracking systems. Another major challenge is the rapid evolution of technologies and market expectations. Machines are becoming increasingly sophisticated, and response times must be shortened to meet customer demands. In this context, traditional maintenance, even in its preventive form, may sometimes appear insufficient to ensure maximum equipment availability​.
Toward a Necessary Transition: The Emergence of New Strategies
Faced with the limitations of corrective and preventive maintenance, new approaches such as predictive maintenance have emerged. These rely on real-time data analysis to anticipate failures before they occur. By combining the best practices of traditional strategies with modern technological innovations, companies can not only reduce costs but also improve the reliability and durability of their equipment. This evolution shows that while traditional industrial maintenance has long been a solid foundation, it is now time to integrate more advanced methods to meet the current and future challenges of the industry​.
Preventive and Predictive Maintenance – Pillars for the Modern Industry
Preventive Maintenance: The Art of Avoiding the Inevitable
Preventive maintenance has become a standard in many industries, far surpassing the reactive approaches of corrective maintenance. The fundamental principle of preventive maintenance is to conduct inspections, cleanings, and scheduled replacements to prevent failures before they occur. This strategy relies on two main approaches: time-based maintenance and usage-based maintenance, both designed to ensure that equipment remains in optimal condition and to reduce the likelihood of unexpected breakdowns​.
Time-Based Maintenance: A Calculated Regularity
Time-based maintenance involves interventions at regular intervals, such as monthly or annual inspections, regardless of the actual condition of the machines. This approach ensures that equipment receives the necessary attention before serious problems arise. For example, replacing components on a fixed schedule, even if they still appear functional, can extend the machine's lifespan and prevent sudden failures​.
Usage-Based Maintenance: Adjusting According to Load
On the other hand, usage-based maintenance occurs based on the operating hours or cycles of the equipment. This approach is particularly useful in environments where machines do not operate continuously, allowing for the frequency of interventions to be adjusted according to the actual use of the equipment. For instance, a machine used sporadically will require less maintenance than one in continuous operation, thereby optimizing resources​.
Predictive Maintenance: When Technology Serves Prevention
With the rapid evolution of technology, predictive maintenance has become a major asset for companies seeking to optimize their operations. Unlike preventive maintenance, which relies on fixed intervals or usage, predictive maintenance uses real-time data to anticipate failures before they happen. By leveraging sensors and advanced monitoring technologies, companies can now continuously monitor the condition of their equipment, detect anomalies, and intervene before the situation deteriorates​.
Technologies at the Heart of Predictive Maintenance
Predictive maintenance relies on a multitude of advanced technologies, such as the Industrial Internet of Things (IIoT), big data analytics, and machine learning. Sensors placed on machines continuously collect data on various parameters, such as vibrations, temperature, and pressure. This data is then analyzed to detect trends or anomalies that could indicate an imminent failure. By identifying these warning signs, maintenance teams can plan targeted interventions, thus minimizing production stoppages and reducing the costs associated with emergency repairs​.
Â
Economic and Operational Benefits of Predictive Maintenance
One of the most significant advantages of predictive maintenance is the reduction in operational costs. By enabling companies to anticipate and prevent failures, this approach drastically reduces unplanned downtimes and the costs associated with emergency repairs. Moreover, predictive maintenance extends the lifespan of equipment, improves reliability, and optimizes the use of human and material resources. Beyond direct savings, this approach also enhances product quality and customer satisfaction by ensuring a more stable and interruption-free production​.
Integrating Predictive Maintenance: Challenges and Solutions
Despite the clear benefits of predictive maintenance, its integration is not without challenges. Implementing real-time monitoring systems and data analysis requires substantial investments in technology and training. Additionally, managing the often massive and complex data collected demands advanced skills in analysis and interpretation. However, companies that overcome these obstacles find themselves with an extremely efficient maintenance system capable of transforming the management of industrial assets​.
Integrating Maintenance into a Modern Industrial Strategy
The Rise of Proactive Maintenance: A New Era for Industry
Proactive maintenance represents the next evolution in industrial maintenance, combining the best practices of preventive and predictive approaches while embracing a more strategic focus. By using root cause analysis and thorough planning, proactive maintenance seeks to eliminate risks before they even manifest. This methodology, often aligned with Reliability-Centered Maintenance (RCM), is highly effective in identifying and addressing critical failure points within an industrial system​.
Reliability-Centered Maintenance (RCM): A Performance-Driven Strategy
RCM is a methodical approach that prioritizes maintenance tasks based on their impact on safety, production, and costs. It focuses on optimizing maintenance processes to maximize the reliability and efficiency of critical equipment. Through systematic analysis, RCM helps develop specific strategies for each piece of machinery, targeting failure modes, and providing tailored interventions. This process involves a deep evaluation of potential failure points and implementing corrective measures to ensure the best possible performance​.
Root Cause Analysis: Tackling Failures at Their Source
A critical component of proactive maintenance is root cause analysis (RCA). This process goes beyond surface-level issues to identify the underlying causes of equipment failures. By addressing these root causes, businesses can prevent recurring issues and improve the overall reliability of their systems. RCA is often integrated into proactive maintenance strategies to ensure continuous improvement in equipment performance​.
Â
Continuous Improvement: A Pillar of Proactive Maintenance
Continuous improvement is at the heart of proactive maintenance. It involves regularly integrating feedback and performance data into the maintenance cycle to refine strategies over time. This includes consistent monitoring of equipment, analyzing past failures, and adjusting maintenance procedures accordingly. With this approach, companies not only maintain but actively enhance the performance and reliability of their equipment as they gather more data and insights​.
The Role of Technology in Proactive Maintenance
The integration of modern technology plays a crucial role in the optimization of proactive maintenance. Tools such as connected sensors, data analysis platforms, and Computerized Maintenance Management Systems (CMMS) allow companies to monitor and manage their equipment more effectively. These technologies provide increased visibility into the condition of machinery, enabling more precise planning of interventions and better prevention of breakdowns. By incorporating these tools into a proactive maintenance strategy, businesses can maximize efficiency and minimize the costs associated with unplanned downtime​.
Challenges of Implementing Proactive Maintenance
Despite its numerous advantages, adopting proactive maintenance presents significant challenges. The complexity of implementing such a strategy requires substantial investment in training, technology, and change management. Additionally, accurate and reliable data is critical for proactive maintenance to be effective, necessitating robust data collection and analysis infrastructure. Collaboration between maintenance teams and other departments within the company is also crucial for successful integration​.
Toward a Fully Integrated Maintenance Strategy
The future of industrial maintenance lies in the full integration of preventive, predictive, and proactive approaches into a cohesive strategy. This integration not only maximizes equipment availability but also optimizes costs and enhances customer satisfaction by ensuring uninterrupted production. By adopting a holistic maintenance approach, companies can prevent failures while creating a more resilient and agile production environment, ready to face the challenges of modern industry​.
Redefining Industrial Maintenance for the Future
In an era where every second of production is crucial, industrial maintenance has never been more essential. Traditional methods have laid the groundwork, but they now reveal their limitations in the face of modern challenges. Preventive maintenance, with its proactive approach, and predictive maintenance, powered by cutting-edge technology, have allowed us to move beyond mere reaction, paving the way for a new era of anticipation.
But the future belongs to those who dare to go further, embracing proactive maintenance strategies that focus on root cause analysis and continuous improvement. This approach doesn't just prevent failures; it aims to eradicate them at their source, transforming maintenance into a powerful driver of industrial performance.
The days of after-the-fact repairs are behind us. Maintenance is no longer just a support service; it is a strategic component essential to maintaining a company's competitive edge. With the rise of technologies like the Internet of Things (IoT), big data analytics, and Computerized Maintenance Management Systems (CMMS), we stand on the brink of a revolution where maintenance becomes synonymous with reliability, resilience, and innovation.
Thus, whether preventive, predictive, or proactive, industrial maintenance is not merely a response to today's challenges. It is an invitation to rethink our infrastructure, embrace innovation, and build a future where machines are not sources of worry but reliable partners in the pursuit of operational excellence. The future of industry will be shaped not only by what we produce but by how we ensure the continuity and performance of our production tools.
This is where the true power of maintenance lies: transforming uncertainty into opportunity and making every intervention a chance to improve, progress, and prepare for the challenges of tomorrow.
Â
DIMO Maint - "Effective strategies for industrial maintenance management," une ressource complète qui discute des stratégies optimales pour la gestion de la maintenance industrielle, y compris la maintenance préventive, corrective et prédictive. Ce site met en lumière l'importance de l'approche prédictive et l'intégration des systèmes de gestion assistée par ordinateur (CMMS).
Sensemore - "What Is Industrial Maintenance? A Complete Overview," un article détaillé qui offre une vue d'ensemble complète de la maintenance industrielle, expliquant les principes de la maintenance préventive, prédictive, et proactive, ainsi que l'importance de l'analyse des causes racines et de l'amélioration continue dans le cadre de la maintenance industrielle moderne.