The 5 Trends Series: 5 Emerging Trends in Industrial IoT in Manufacturing to Watch in 2024
- Ali
- 17 sept. 2024
- 5 min de lecture
Dernière mise à jour : 18 sept. 2024
Ali.
18/09/2024
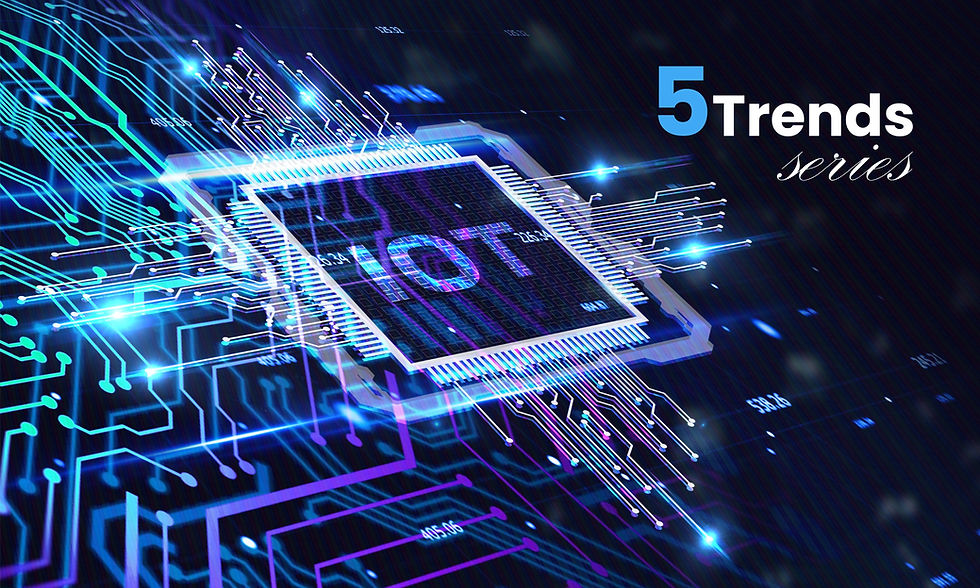
Industrial IoT in Manufacturing
The Industrial Internet of Things (IIoT) is reshaping how factories operate, paving the way for smarter automation, increased efficiency, and real-time decision-making. As we head into 2024, IIoT continues to evolve, bringing new opportunities to optimize manufacturing processes. Companies that embrace these emerging technologies can not only boost productivity but also remain competitive in a rapidly changing global market.
In this article, we will explore five key trends to watch in the IIoT space for 2024. These trends highlight how technology is shaping the future of smart factories and transforming the way industrial operations are managed.
Trend 1: Advanced Predictive Maintenance
One of the most significant applications of IIoT in manufacturing is predictive maintenance. By utilizing real-time data from sensors embedded in machinery, manufacturers can anticipate equipment failures before they happen. Predictive maintenance allows for data-driven insights that lead to more efficient maintenance schedules, reducing costly unplanned downtime and extending the lifespan of critical equipment.
In 2024, we expect this trend to evolve even further as machine learning algorithms become more advanced. These algorithms can now analyze massive amounts of data collected from IIoT devices, detecting patterns that signal potential issues long before they disrupt production. This shift from reactive to proactive maintenance is not only improving operational efficiency but also lowering maintenance costs and minimizing waste.
Additionally, predictive maintenance empowers manufacturers to allocate resources more effectively, only servicing machines when necessary, rather than adhering to rigid, time-based schedules. As IIoT technology continues to mature, expect even more sophisticated systems that will integrate seamlessly into existing manufacturing environments, creating smarter factories with higher reliability and output.
Trend 2: Increased Adoption of 5G Connectivity
The adoption of 5G networks is revolutionizing the Industrial Internet of Things, providing the infrastructure necessary for faster, more reliable communication between machines. 5G’s ultra-low latency and high-speed data transmission capabilities are enabling manufacturers to implement real-time monitoring and control of their operations like never before.
In 2024, 5G will play an even more critical role as manufacturers increasingly rely on connected devices to automate processes and enhance efficiency. With 5G, factories can support a higher density of IIoT devices, ensuring seamless communication across all systems, from production lines to quality control. This advancement is particularly important for mission-critical applications, where even the slightest delay in communication can disrupt operations or compromise safety.
Moreover, 5G’s improved bandwidth facilitates the use of technologies like augmented reality (AR) for maintenance and training, allowing workers to access real-time data and support in remote environments. As the rollout of 5G continues globally, manufacturers will have greater flexibility to deploy IIoT solutions at scale, driving the next wave of smart factory innovations.
Trend 3: Enhanced Cybersecurity Protocols
As the Industrial Internet of Things (IIoT) grows, so do the security risks associated with connected devices and data. In 2024, cybersecurity will be a major focus for manufacturers implementing IIoT solutions. With more machines, sensors, and systems connected to networks, the attack surface for cyber threats has expanded, making robust security measures more essential than ever.
Manufacturers are now integrating advanced cybersecurity protocols specifically designed for IIoT environments. This includes securing data transmission between devices, protecting sensitive information from unauthorized access, and using real-time monitoring to detect and respond to threats quickly. Technologies like blockchain are also being explored to create tamper-proof logs of industrial operations, ensuring data integrity and accountability.
Another key development in 2024 is the increased use of AI-driven cybersecurity. These AI systems can analyze network traffic, identify unusual patterns, and autonomously respond to potential threats, minimizing the risk of downtime or data breaches. While the IIoT ecosystem expands, the focus on cybersecurity will not only protect infrastructure but also instill confidence in businesses as they embrace more connected technologies.
Trend 4: Edge Computing in Industrial IoT
Edge computing is rapidly gaining traction in the landscape, allowing data processing to occur closer to the source—on the factory floor—rather than relying solely on cloud computing. This approach reduces latency, increases efficiency, and enables faster decision-making, which is crucial for real-time applications in manufacturing.
In 2024, edge computing will become a standard feature in smart factories as manufacturers aim to optimize their IIoT systems. By processing data locally at the “edge,” companies can reduce the bandwidth required to send vast amounts of information to centralized cloud systems. This is especially important in environments where time-sensitive decisions are necessary, such as in automated quality control or production line adjustments.
Additionally, edge computing enhances the resilience of IIoT systems. Even if cloud connectivity is lost or unstable, critical operations can continue without disruption, as data is processed on-site. This decentralization of computing power helps improve overall system reliability and ensures continuous operation in high-demand manufacturing settings.
As more industries embrace edge computing in their IIoT infrastructure, the ability to run complex analytics and make real-time adjustments on the factory floor will empower manufacturers to drive innovation and maintain competitive advantages.
Trend 5: Digital Twins and Simulation
The use of digital twins in manufacturing is set to grow even more prominent in 2024. A digital twin is a virtual replica of a physical system—whether it’s an entire factory, a specific machine, or a production line. By creating a digital twin, manufacturers can simulate, monitor, and optimize processes in real time, leading to significant efficiency gains.
In 2024, digital twin technology will see further advancements, enabling manufacturers to run simulations that help predict outcomes, test changes in production lines, or identify potential bottlenecks without interrupting actual operations. These simulations allow manufacturers to fine-tune operations, reduce downtime, and improve decision-making, all while saving costs on physical prototypes or unnecessary adjustments.
Additionally, digital twins are becoming smarter with the integration of AI and machine learning, which enables these systems to learn from real-time data and continuously improve. By combining IIoT sensors with AI-powered digital twins, manufacturers can create self-optimizing systems that automatically adjust to new conditions, improving overall productivity.
This technology not only provides a deeper understanding of current operations but also plays a pivotal role in planning for future changes. As more manufacturers adopt digital twin technology, the potential for innovation and process optimization in the industry will only continue to expand.
Summary
As we look ahead to 2024, the Industrial Internet of Things (IIoT) is set to play an even larger role in transforming the manufacturing landscape. From advanced predictive maintenance that reduces downtime to 5G connectivity that enables faster communication, manufacturers are becoming more connected and efficient. Enhanced cybersecurity protocols are protecting these increasingly complex systems, while edge computing is speeding up data processing on the factory floor. Finally, the evolution of digital twins allows for greater optimization through real-time simulations and smarter, self-improving systems.
Together, these trends signal a future where manufacturing is more intelligent, responsive, and capable of adapting to new challenges. Companies that embrace these advancements will be well-positioned to stay competitive in an ever-evolving global market.
Forbes. "How IIoT is Revolutionizing the Manufacturing Industry."
McKinsey & Company. "The Rise of Digital Twins in Manufacturing."
World Economic Forum. "The Impact of 5G on Industry 4.0."
Deloitte. "Predictive Maintenance in Manufacturing: A Game Changer."
Cisco. "Enhancing Cybersecurity in the Age of IIoT."